University of Arizona
IceBank energy storage improves the power efficiency of cogeneration at one of the largest thermal energy storage installations in the world.
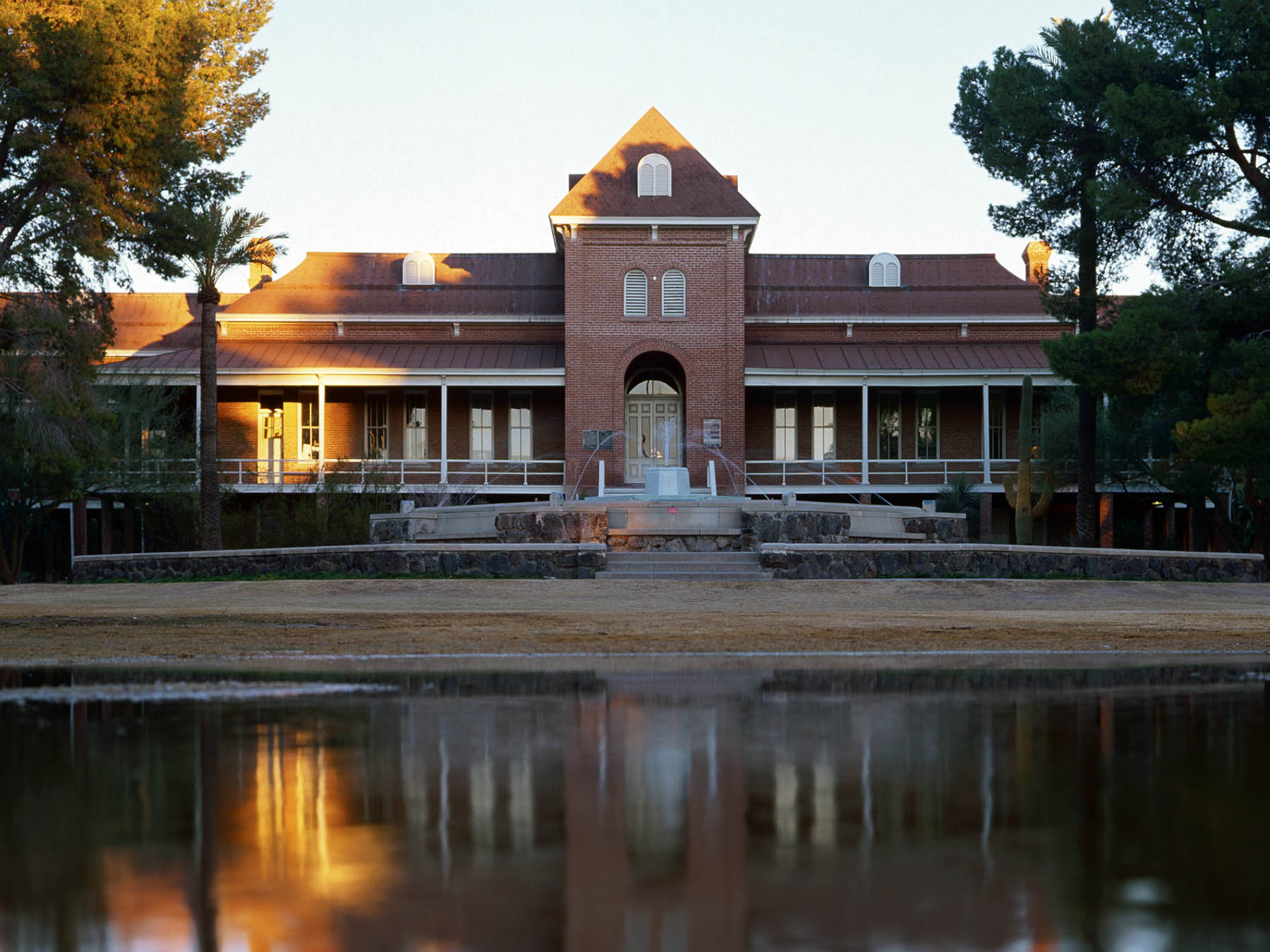
Project Facts
- 216 buildings on a 378 acre campus
- Student population of over 37,000
- $38,000 monthly savings
- When It's Hot Outside, Ice Helps the UA Stay Cool
- Thermal energy storage is a UA success
- Download the Case Study
OVERVIEW
In the Report of the National Energy Policy Development Group, The National Energy Policy defined cogeneration as “the production of electricity and another form of energy (such as heat or steam) used for industrial, commercial, heating or cooling purposes.” Turbines, which are like powerful engines, produce both the heat and the power. This combined generation can increase the efficiency of the fossil fuel-based power plants from an average of 35-40% to over 80%.
In addition to better efficiency, cogeneration offers reliability and lifecycle cost advantages. Cogeneration is more reliable than merchant generators for electrical service because it is committed exclusively to electrical needs of the customer. Source efficiency is improved because cogeneration assets are in close proximity to where it is consumed, which dramatically minimizes the energy losses that are normally incurred in having to transport electricity over long distances. This efficiency is especially applicable for large consumers such as universities and hospitals since that have a need for large amounts of heat, most of the time.
Cogeneration designs that can effectively level the heat and power loads near full load are most ideal since turbines that operate near full load are more efficient. According to the California Energy Commission, “When less than full power is required from a gas turbine, the output is reduced by raising the turbine inlet temperature. In addition to reducing power, this change in operating conditions also reduces efficiency. Part load efficiencies (50%) load are approximately 25% lower than full-load efficiencies.”
CHALLENGE
So what can be done when heat and power loads are not level? This was the quandary faced by the University of Arizona (Tucson). Five years ago, the University installed two very sophisticated and ambitious cogeneration plants. As the University expanded its campus, daytime electrical needs allowed full use of their Solar (manufacturer) gas-fired turbines, which in turn created sufficient heat during the day. At night, however, when the rest of the campus’s electrical requirements were reduced, the University Medical Center still needed heat for sterilization, laundry, etc. So electricity was not only being produced under less efficient conditions, two ancillary Rentech (2-50 Kblbs/hr) boilers were needed to produce sufficient heat to meet hospital requirements.
“Eventually the CALMAC system was chosen because of its tanks’ non-corrosive material, the ability to isolate modules in groups of 3 (IceBank® tank model 1500C), the mobility of the tanks, their ease of installation and the ease of maintenance and repair,” notes Gordon Bush, the U of A Project Manager and Chilled Water Staff Technician
This dilemma was rectified by the innovative minds of central plant managers, Gordon Bush and Marianne Deutsch as well as Ned Morris, Trane senior sales engineer. The mechanical, electric, and civil design was the responsibility of Henry Johnstone at GLHN Architects and Engineers. Together, they created a simple and innovative solution relative to this obvious waste.
SOLUTION: ENERGY INDEPENDENCE
The team opted to resolve their quandary by creating a useful application for nighttime electricity in order to get the needed heat as a bi-product of operating the turbines at night. Ice storage was explored as a viable solution for this dilemma.
Essentially, ice storage uses ice produced at night to cool buildings the following day. Ice storage serves the useful purpose of providing a nighttime load for the cogeneration plant (the ice making chillers require electricity to operate) as well as to provide extra cooling capacity to meet cooling loads on the next day. Other unique benefits of ice storage include giving the University added flexibility during equipment downtime for scheduled chiller and turbine repair and maintenance.
Ice storage technology is both common and unique. It is common since it does for cooling what a domestic water heater does for hot water. As a unique cooling option, ice storage is the only air-conditioning system that utilizes plentiful nighttime produced electricity to generate and store daytime cooling. As a result, it provides the key benefit of lowering greenhouse gas emissions along with reducing the cost of cooling from on-peak electric demand. In utility-driven cooling applications, ice storage provides a nighttime electric load to store cooling. In the U of A cogeneration application however, ice storage not only stores the cooling, it also provides a nighttime electric load in order to produce steam for use by the University Medical Center.
With a student population of over 37,000 and supporting approximately 216 buildings on a 378 acre campus, the University facility infrastructure consists of three central plants: the Central Heating Refrigeration Plant, (CHRP) the Central Refrigeration Building (CRB) and the Arizona Health Sciences Center (AHSC). These plants are hydraulically connected with all distribution and production controlled and optimized by a Trane Tracer® Summit building automation system. This means that chilled water produced in any of the plants can be delivered to any corner of the campus.
The CHRP was built in 1950 and has 8,500 tons of centrifugal refrigeration chilled water capacity along with 154,000 pph of 125 psi steam capacity from three gas-fired boilers. It also has a 6.5 MW, gas-fired turbine generator with an auxiliary 1.7 MW steam turbine generator that produces electricity for the campus grid along with 33,000 pph of 125 psi steam from the Turbine Exhaust Heat Recovery Steam Generator (HRSG.)
The second central plant, built in 1968, is the AHSC. It has 7,200 tons of centrifugal refrigeration chilled water capacity along with 70,000 pph of high-pressure steam capacity, which is produced by two gas-fired boilers and 24,000 pph high-pressure steam from a 4.5 MW gas turbine at HRSG.
The CRB, is of 1988 vintage and is the home of the Ice Storage System. When its three ice chillers make ice, the system has 15,650 tons of centrifugal refrigeration chilled water capacity. However, when the chillers produce chilled water, that capacity is increased to 17,000 tons.
RESULTS
The ice storage system (also known as the thermal storage project or ice plant) is powered by a Combined Heat and Power (CHP) system located at the AHSC plant, that supplies electricity to three Trane CenTraVac ice chillers,” says Ned Morris Trane’s local representative. “These chillers make ice at 910 tons and 0.783 kilowatt/ton. They freeze water in the 156 storage tanks which are discharged on demand, providing 23,400-ton hours of capacity or 3,120 tons for 7.5 hours. We often accelerate the discharge to as high as 3,500 tons during peak hours, further reducing electric demand charges.”
The use of ice storage for recovering turbine heat means the AHSC Plant Turbine is now loaded during off-peak hours, thereby reducing the higher natural gas cost for boiler steam. In turn, chilled water costs are kept to a minimum by reducing the number of chillers that need to run at peak-demand periods.
When fully loaded, the Deltak Heat Recovery Steam Generator (22 KPlbs/hr) produces 24,000 pph of high-pressure steam, most of which is used by the AHSC as well as by the University Medical Center and its surrounding buildings. The auxiliary steam turbine can be used to generate electricity during periods of excess steam production, if the chilled water load allows.
The ability to choose gas or purchased electricity, combined with the ability to move or reduce electric demand with ice storage, provides tremendous negotiating power with the local utility suppliers.
“Shaving this peak represents up to a $38,000 monthly savings to the University,” notes Marianne Deutsch.
Ice is produced at the CRB during the evening and at night and is melted to produce chilled water during the day. However, during winter evenings, when the campus chilled water load falls below 5,000 tons, to the resultant electric load on the AHSC 4.5-MW Solar turbine is unable to meet the University Medical Center and Sciences Center buildings’ steam demand. In these situations, the ice chillers are brought on line to produce ice, raising the electrical load on the turbine and thus producing the needed steam.
With ten years of steady investment in chilled water distribution infrastructure, the University has created a chilled water grid with less than a 12 psig pressure differential across the 1.3 mile campus diameter. As a result, chilled water produced by the ice storage system can be distributed across campus during the day to displace production by any chiller connected to the utility’s electrical grid and distribution loop. “Shaving this peak represents up to a $38,000 monthly savings to the University,” notes Marianne Deutsch.
In addition, prior to ice storage, the chillers needed to “cycle” in order to meet fluctuating cooling loads. With ice storage, the chillers can run constantly at the same level of output, which, in turn, optimizes the turbine’s efficiency and extends the life of the chillers.
U of A representatives investigated ice storage by visiting several installations that use this technology, including CALMAC’s installation at Shell Point, a retirement community in Ft. Meyers, Florida. “Eventually the CALMAC system was chosen because of its tanks’ non-corrosive material, the ability to isolate modules in groups of 3 (IceBank® tank model 1500C), the mobility of the tanks, their ease of installation and the ease of maintenance and repair.” Notes Gordon Bush, the U of A Project Manager and Chilled Water Staff Technician, “An additional consideration was the simplicity and modular nature of the CALMAC system. We started on June 1, 2004 and produced our first batch of ice on July 1, 2004. We have had ice available everyday, without exception since then. We would not have made this tight schedule without our piping partner, Sun Mechanical headed by Scott Candrian."
SUMMARY
The original plans called for 23,400 ton-hours (3,000 tons for 8 hours at 39 degrees), however up to 23,400 ton-hours from the system at a higher discharge temperature for longer melting periods was delivered. Today the system relies on 156 tanks at about 150 tons/hour each.
The original system has worked so well, we have a new project under construction and have ordered another 49 tanks and a 1250-ton Trane chiller, for an increase of 7,350 ton-hours of ice storage at the CHRP. The 1250 ton chiller can be used for both ice or chilled water generation.
University of Arizona’s decision to use ice storage involved many factors including economic and environmental. While ice storage is generally touted as a cost-saving cooling option, in this instance, ice storage also provided the unique ability to dramatically increase cooling capacity while improving the overall efficiency of the plant. To the University, these concerns were of paramount importance.
Ice storage also provides the University with greater flexibility in chiller and turbine maintenance scheduling, yet another benefit of base loading the turbine generation.
Ice Storage contributes to N+1 redundancy as well, an intrinsic concern for any engineer. While the University has sufficient capacity in place to meet its current daytime, peak-cooling load, ice storage serves in a standby capacity. Furthermore, should any chiller become inoperative, another chiller can be called into action without disruption to the service.
COMPUTER MODELED
“The efficient integration of all these loads could be a logistical nightmare,” explains Marianne Deutsch. “That’s why we recently installed highly sophisticated software to help optimize our energy consumption.” This software enables plant operators to monitor, control and evaluate energy flows and costs.
“Ice storage has given us the flexibility we needed to maximize our efficiency with the production and use of energy,” Marianne Deutsch added.
The software creates up to 48 possible operating scenarios with different mixes of plants, chiller, boilers, pumps, towers and ice storage. Operators can then choose the optimal scenario on the basis of cost, maintenance schedules, campus building schedules and the weather forecast. “Ice storage has given us the flexibility we needed to maximize our efficiency with the production and use of energy,” Deutsch added.
Saving energy, reducing costs and lowering polluting emissions are an integral part of the University of Arizona’s mission of providing a comfortable, affordable learning experience for its students. University’s facility managers are charged with maximizing the utilization of available resources and are committed to co-generation. Faced with having to provide heat to the hospital, they were also faced with having to co-generate that heat. Ice storage met that requirement by consuming the co-generated electricity, leveling the load and improving efficiency and lowering emissions.